By Molly George
Photos by Miranda Rico
From our June 2024 issue
On a recent afternoon in a whitewashed lab in Portland’s Roux Institute, the nozzle inside a massive, whirring 3D printer was squeezing out a plastic surfboard like frosting from a pastry bag. When the board, known at this early stage as a “blank,” emerges, it’ll sport a diamond-lattice design that Blueprint Surf founders Luke Diehl and Mike Ballin will sand smooth, then coat with multiple layers of epoxy in a rented South Portland garage. On the translucent finished product, the tessellated pattern shows through like veins on a leaf, and when light hits the glassy surface — at sunrise, say, with waves rolling in at a local beach — it glows.
The idea of 3D printing surfboards isn’t new. Innovators around the world have been working for years to create eco-friendly alternatives to typical boards, which are made from non-recyclable polyurethane foam that’s topped with petroleum-based fiberglass and polyester or epoxy resin. Instead, 3D printing produces an object from a digital model by layering melted material into a desired shape. Some companies have fabricated slick 3D-printed surfboards with recycled plastics and epoxies partially derived from plant-based materials. Diehl and Ballin have done that too, but they are the first to do it in the U.S., and the first to use the technology to design boards specifically tailored to New England’s variable waves — from post-hurricane rollers to the usual muddled chop. Their boards are slightly heavier than conventional foam ones, the better to slice through soupy conditions, and have proven themselves durable in Maine, where 3D-printed boards have yet to catch on.
Two years ago, Diehl, an engineer and avid surfer who’d been toying with the idea of 3D printing a surfboard for years, recruited fellow surfer Ballin, a recent Colby College grad with a degree in environmental studies, to help in the endeavor. Their first effort, printed by a third-party contractor, came in four pieces with the latticework oriented in a horizontal direction prone to breakage. Their second attempt filled with water soon after they launched it off Scarborough’s Higgins Beach, but the momentary ability to catch a wave felt like progress.
Last summer, Diehl and Ballin partnered with Northeastern University’s Roux Institute, which offers graduate and research programs in advanced technologies. Ballin assembled a 3D printer capable of churning out boards up to six feet long (larger models are printed in two pieces and glued together)in the institute’s composites lab, where grad students are conducting research the Blueprint team hopes to use to refine current designs and engineer new ones. Diehl and Ballin have also committed themselves to using recycled-plastic filament (which gets melted down inside the machine) for their blanks and epoxy coatings containing resins extracted from corn, soybean, and other plant byproducts.
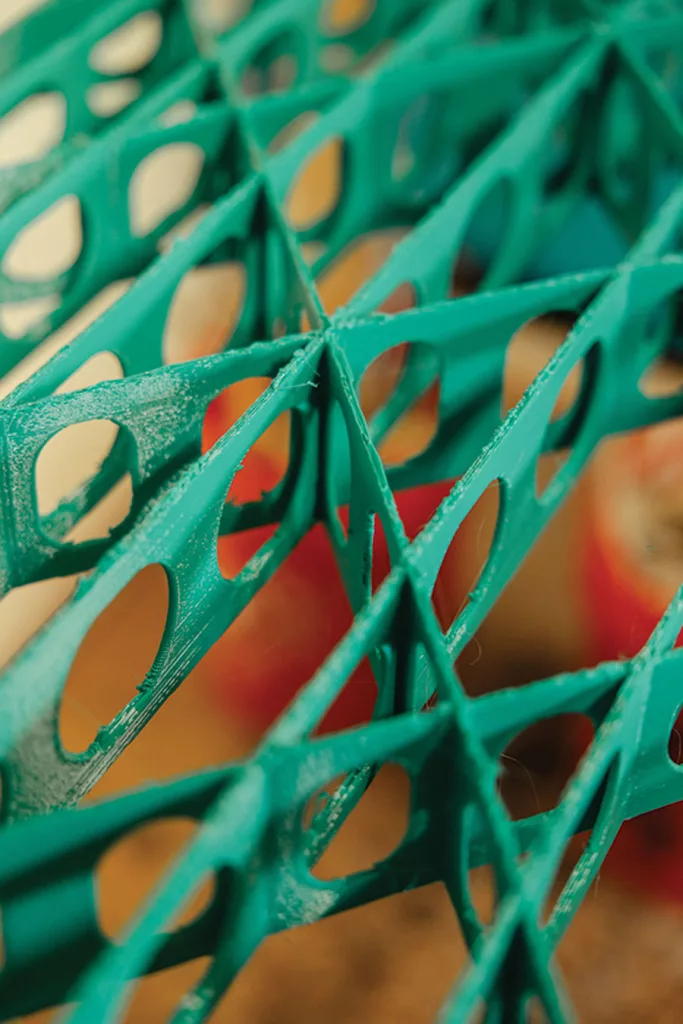
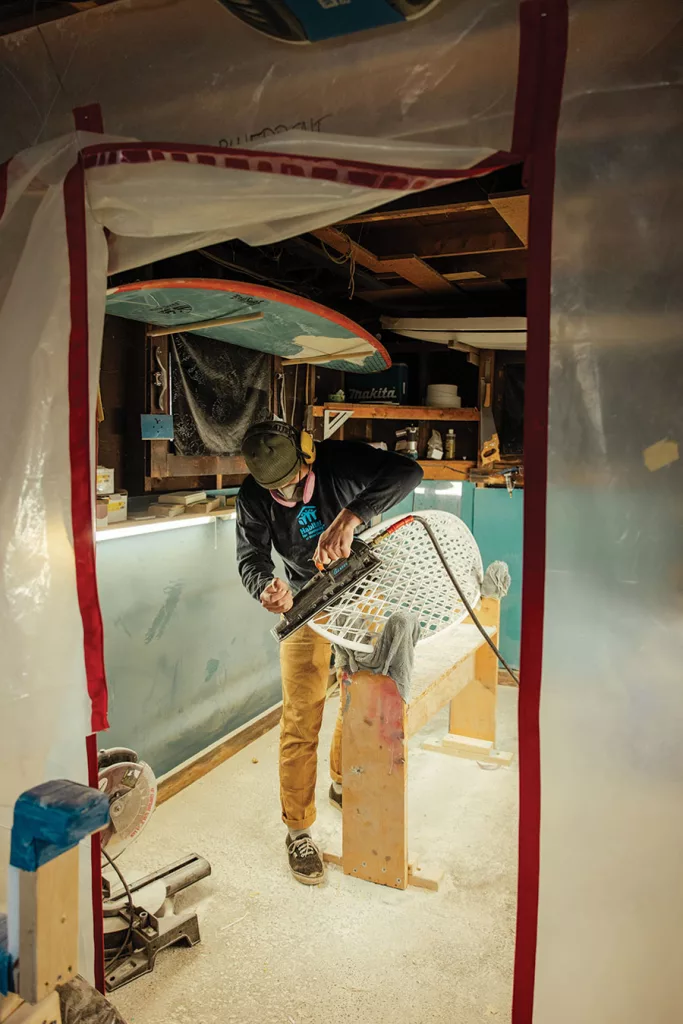
Blueprint Surf currently sells a versatile, year-round shortboard (six to seven feet long) that can handle swells up to eight feet high and a squatter model designed for smaller summer waves, with prices starting at $700 (in general, new surfboards cost anywhere from several hundred to several thousand dollars, putting Blueprint somewhere in the middle of that range). A more maneuverable “fish” shortboard with a forked tail and a classic, stable longboard are both under development. But building new models around the openwork plastic frame presents unique challenges. For example, when Ballin tested a fish prototype in El Salvador last winter, the internal structure, made too thin, collapsed under his weight. “It was like surfing on a pool noodle,” Ballin says.
Still, 3D modeling offers tantalizing advantages. Since each board is made-to-order, the weight and flexibility can be customized according to riders’ preferences. To cut down on the amount of material they use, Diehl and Ballin are collecting leftover plastic from the supports the 3D printer produces as it builds surfboard blanks, and they plan to use those leftovers to create more blanks. They’re also experimenting with polypropylene filament derived from recycled fishing nets. “This area has a cool legacy of building beautiful, sustainable, handcrafted gear,” Diehl says. “Our 3D printing sounds high-tech, but we feel like we’re honoring that tradition of high-quality, handmade gear that people can love for a long time.”