By Charlie Pike
From our May 2025 issue
On the University of Maine campus, a 50,000-square-foot factory is in the works where massive robotic arms, supervised by drones, will assemble 3D-printed houses, boats, and more. It sounds like something out of science fiction. But Habib Dagher believes the era of fully automated factories is here. Since founding UMaine’s Advanced Structures and Composites Center, in 1996, Dagher and his colleagues have used the world’s largest 3D printer to create the world’s largest 3D-printed boat and first 3D-printed house made from bio-based materials, while churning out dozens of other inventions, like an inflatable carbon-fiber bridge that can be transported to a job site in a backpack. The new $82 million Green Engineering and Materials building, slated to open late next year, will house the Factory of the Future, a 3D-printing manufacturing hub staffed with robots that will enable Dagher’s team to scale up production of units to combat the housing crunch, streamline boatbuilding, develop technologies to address renewable energy and infrastructure needs, and who knows what else. “We’re going where no one has gone before,” Dagher says. “The equipment that’s going into the Factory of the Future does not exist anywhere in the world. We’re designing it as we speak.”
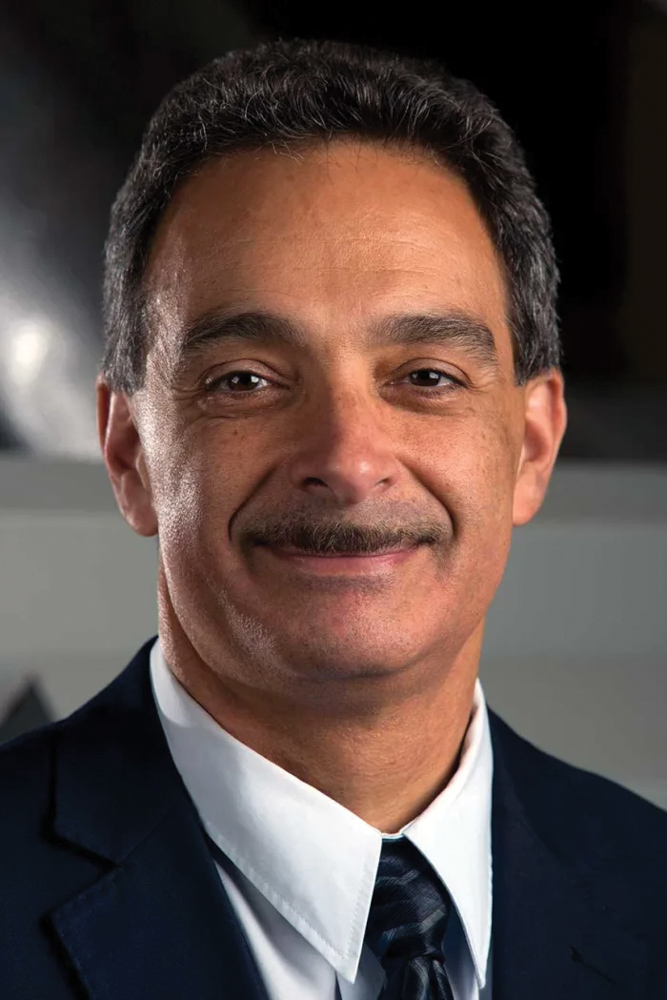
What will manufacturing look like at the Factory of the Future?
Picture a 3D printer. There will be a robot operating it, layering materials to produce a truss, walls, and floors for a house. Then there’s a robot behind it that’s placing wiring or putting wood-fiber insulation into walls. These robotic systems can position themselves in space and know what’s around them. And know what their job is, like hanging kitchen cabinets or painting. They are monitored by drones that are scanning the workspace, recognizing mistakes, and feeding data into a high-performance computing environment that tracks each part of the house as it’s being produced. That information becomes available to the robots, making them self-aware. So the machines are sensing what they’re doing as they work and can adjust the manufacturing process to react to mistakes and make sure those mistakes don’t happen again.
Do you worry about robots replacing human workers?
We’re not looking at displacing the current home-building technology; we’re looking at supplementing it. We’re not producing enough homes for people because we don’t have the people to build them. We have a big deficit, and I see the Factory of the Future working hand-in-hand with the housing industry we have today. This technology also has the potential to address challenges, particularly labor shortages, in boatbuilding yards. Where is the workforce going to come from that knows how to run these types of Factories of the Future? We’re going to train people and develop new educational programs so students can learn how to do this work, and then take that knowledge to private industries and implement it.
What are some benefits for consumers?
We’re using our current facility to produce a neighborhood for the unhoused population in Bangor. We’re working with the state and a nonprofit group to build nine homes. With the Factory of the Future, we can scale that up. For the average consumer, can you get on a computer and say, ‘I want a 600-square-foot, one-bedroom home?’ Then look through 40 or 50 designs, find one you like, and say, ‘I want the living room to be two feet wider. I want the roof to be curved.’ And what if we could deliver it to you in a few weeks? If you want a 20- or 30-foot vessel, can you come pick it up in a couple of days? That’s the kind of technology we’re looking to develop.
What about the environmental benefits?
The homes and boats we’re producing are made with sawmill waste and other bio-based materials and recycled resins. They’re 100 percent recyclable, and we’re looking at getting to near-zero waste during the manufacturing process. About a million tons of wood waste comes from Maine sawmills every year. That’s enough material to produce 100,000 600-square-foot homes. The use of bio-based and recycled materials also has the potential to address supply-chain challenges and reduce material costs. And what’s really exciting? Say your children or grandchildren or great-grandchildren don’t want your home years from now. Guess what? They can take the home, grind it up, and we can print something else with it.